Some of these U.S. Military Technical Manuals sell for a $ each on other sites .. ELECTRIC MO DRIVEN, AC, V, 3 PHASE, 60 HZ; SINGLE OPERATOR, 50/6 (THERM-AIR MODEL CV) () AND V, 3 TM , 10, AIR CONDITIONER, COMPACT VERTICAL: V, 3.
Table of contents
- Functional Users Manual for The Army Maintenance Management System (TAMMS) - PDF
- We are offering our package for only $45 which includes free shipping also.
- about of parts
This position will contain one of the following maintenance codes: Direct support or aviation intermediate is the lowest level that can do complete repair of the item. General support is the lowest level that can do complete repair of the item. Specialized repair activity designate the specialized repair activity is the lowest level that can do complete repair of the item. Depot is the lowest level that can do complete repair of the item. No repair is authorized. No parts or special tools are authorized for the maintenance of a B coded item. However, the item may be reconditioned by adjusting, lubricating, etc.
Recoverability codes are assigned to items to indicate the disposition on unserviceable items. The recoverability code is entered as follows: When unserviceable, condemn and dispose of the item at the level of maintenance shown in 3rd position of SMR Code. When uneconomically repairable, condemn and dispose of the item at organizational or aviation unit level. When uneconomically repairable, condemn and dispose of the item at direct support or aviation intermediate level. When uneconomically repairable, condemn and dispose of the item at the general support level. When beyond lower level repair capability, return to depot.
Condemnation and disposal of item not authorized below depot level. Condemnation and disposal not authorized below specialized repair activity SRA. Indicates the primary number used by the manufacturer individual, company, firm, corporation, or Government activity , which controls the design and characteristics of the item by means of its engineering drawings, specifications, standards, and inspection requirements to identify an item or range of items. When you use a NSN to requisition an item, the item you receive may have a different part number from the part ordered.
This column includes the following information: When density of equipments supported exceeds density spread indicated in the basis of issue, the total authorization is increased proportionately. The QTY quantity per figure column indicates the quantity of the item used in the breakout shown on the illustration figure, which is prepared for a functional group, subfunctional group, or an assembly.
A V appearing in this column in lieu of a quantity indicates that the quantity is variable and the quantity may vary from application to application. Explanation of Columns Section IV. When using this column to locate an item, ignore the first four digits of the NSN. However, the complete NSN should be used when ordering items by stock number. The item number identifies the item associated with the figure listed in the adjacent FIG.
This item is also identified by the NSN listed on the same line. Part numbers in this index are listed by part number in ascending alphanumeric sequence i. Indicates the primary number used by the manufacturer individual, firm, corporation, or Government activity , which controls the design and characteristics of the item by means of its engineering drawings, standards, and inspection requirements to identify an item or range of items. The item number is that number assigned to the item as it appears in the figure referenced in the adjacent figure number column.
Figure and Item Index. This column lists the NSN for the item. Indicates the primary number used by the manufacturer individual, firm, corporation, or Government activity , which controls the design and characteristics of the item by means of its engineering drawings, specifications standards, and inspection requirements to identify an item range of items.
- Search for MEPA.
- Susie and Me Days: Joy in the Shadow of Dementia;
- When a Woman Loves a Man: Poems.
Until the NSN s are established and published, submit exception requisitions to: How to Locate Repair Parts. Using the table of contents, determine the assembly group or subassembly group to which the item belongs. This is necessary since figures are prepared for assembly groups and subassembly groups, and listings are divided into the same groups. Find the figure covering the assembly group or subassembly group to which the item belongs.
Identify the item on the figure and note the item number. Refer to the Repair Parts List for the figure to find the part number for the item number noted on the figure. Using the National stock number or the part number index, find the pertinent National stock number or part number. The part number in the Part Number index are listed in ascending alphanumeric sequence. After finding the figure and item number, verify that the item is the one you re looking for, then locate the item number in the repair parts list for the figure Abbreviations. Panel-Chassis Assembly 1A1 Sheet 1 of 5.
Panel-Chassis Assembly 1A1 Sheet 2 of 5. Panel-Chassis Assembly 1A1 Sheet 3 of 5. Panel-Chassis Assembly 1A1 Sheet 4 of 5. Panel-Chassis Assembly 1A1 Sheet 5 of 5. Chassis Assembly 1A1A2 Sheet 2 of 3. Tuning Drive 1A1A3 Sheet 2 of 2. Frequency Standard Module 1A3 Sheet 1 of 2. Frequency Standard Module 1A3 Sheet 2 of 2. Transmitter lf and Audio Module 1A5 Sheet 1 of 2. Frequency Dividers Module 1A6 Sheet 1 of 2. Frequency Dividers Module 1A6 Sheet 2 of 2. Receiver lf Module 1A7 Sheet 1 of 2.
Translator Module 1A8 Sheet 1 of 2. Receiver Audio Module 1A10 Sheet 1 of 3. Receiver Audio Module 1A10 Sheet 2 of 3. Receiver Audio Module 1A10 Sheet 3 of 3. Chassis-Panel Assembly 2A1 Sheet 1 of 2. Chassis-Panel Assembly 2A1 Sheet 2 of 2. Chassis Assembly 2A1A1 Sheet 1 of 4. Chassis Assembly 2A1A1 Sheet 2 of 4. Chassis Assembly 2A1A1 Sheet 3 of 4. Chassis Assembly 2A1A1 Sheet 4 of 4.
Drive, Turret 2A2A2 Sheet 1 of 4. Drive, Turret 2A2A2 Sheet 3 of 4. Drive, Turret 2A2A2 Sheet 4 of 4. Antenna Coupler Assembly 2A3 Sheet 1 of 2. Antenna Coupler Assembly 2A3 Sheet 2 of 2. Case Assembly 2A6 Sheet 2 of 4. Case Assembly 2A6 Sheet 3 of 4. Case Assembly 2A6 Sheet 4 of 4. Relay Assembly 2A7 Sheet 1 of 2. Relay Assembly 2A7 Sheet 2 of 2. Driver Assembly 2A8 Sheet 1 of 3. Driver Assembly 2A8 Sheet 2 of 3. Driver Assembly 2A8 Sheet 3 of 3.
Film-Tech The information contained in this Adobe Acrobat pdf file is provided at your own risk and good judgment. These manuals are designed to facilitate the exchange of information related to cinema. Description and Specifications Contents 1. The contents for this script were developed by a review group of industry experts and were based on the best available. All Rights Reserved Even though the K3 s audio output. Drawings and general provisions of Contract, including General and Supplementary Conditions and Division-1 Specification.
Spare parts list Edition Valid for serial no. A Variable Capacitor is one whose capacitance may be intentionally and repeatedly changed mechanically. October 10th by: These kits are designed for wireless. Only qualified personnel familiar with DC drives and associated machinery should plan or implement. This is the parts list for the AFE.
When looking up part numbers, always check the complete model and serial numbers to be certain of ordering the correct parts. The Air Cooled model has also been manufactured. About this Manual We ve added this manual to the Agilent website in an effort to help you support your product. This manual is the best copy we could find; it may be incomplete or contain dated information. The increase in signal by an amplifier is. Parts List For printer models: RF Training Kits Presenter: Cooper Liu, Engineer Department: Frog sounds micro telegraph transceiver kit instructions Brief introduction This is a very small 40 meter band magnitude telegraph micropower transceiver, a 12V DC power supply, spread the good can be.
To understand the concept of HI-FI audio equipment To generate a frequency response curve for an audio. Box Clinton, MI U. A Introduction Fig 1: Army MARS aar2ey usarmymars. If you have any questions concerning. The following is a breakdown description of the. Vehicles are equipped with air bag supplemental restraint system.
Before attempting any repairs involving steering. The person in charge and responsible for the safety and operation of the equipment and operator will sign in that case. Passengers of equipment used as taxis do not sign in this column. In that situation, the dispatcher signs this column when the equipment returns. Signature in this block shows that when an official user has completed the mission with the vehicle and driver, the senior occupant assumes vehicle responsibility.
Note the change of days. Draw a line through the next open line under the last entry of a day. The operator or user reports any unusual or abnormal situations. This includes accidents, breakdowns, unplanned stops or changes in location, and so forth. Any unusual operations and faults on the equipment go on the DA Form b. The operator will list any oil added to equipment or components under AOAP. Fuel added will be logged if required locally. Enter the word Exercised when low usage equipment is exercised.
For equipment you manage by registration number, enter the registration number. If the equipment will be dispatched with a trailer or other item, include the item s bumper or administration number. More than one component on an end item can be under AOAP; for example, the engine and transmission. When that occurs, divide the OIL block into sections, one for each component covered, and enter the oil added for each separately. The dispatcher prints the name or names of the operator or operators of the equipment. This normally happens when an operator becomes sick or overly tired.
For convoy or other long operations where an operator and assistant operator switch at each rest stop, show a change in operators only when destinations or date entries are made. Enter the time when the equipment was released by the dispatcher. The dispatcher enters the hours from the hourmeter when the equipment is dispatched. You must enter the beginning point of the dispatch, the ending point, any off post travel stops, or the major operating point.
Enter first name, middle initial, last name. This includes accidents, breakdowns, unplanned stops, or changes in location, etc. When the equipment is not operated for more than 1 day in a row, you may use one line to cover the combined time. Additional Report to entries may be needed. Note if an extended dispatch will be so long that a form may be completed, another DD Form may be used as a continuation sheet. Enter the equipment s registration or serial number and admin number at the top of the form. Print Continuation in the upper left hand corner of the form.
Then make normal entries as required. The date will be reflected as two places for the year, two for the month, and two for the day. The dispatcher enters the equipment s bumper number. If the equipment will be dispatched with a trailer, or other item, include that item s bumper or administration number.
For equipment under the ACAP, the dispatcher will keep a running total of oil added to the equipment. This normally happens when an operator becomes sick overly tired, etc. Enter the date yymmdd. These blocks will be used to show starting and stopping times for each operation. For equipment without an hourmeter, enter the 24 hour clock time e.
For equipment with an hourmeter, enter the hours on the equipment when you started this operation. For equipment with an hourmeter, enter the hours on the equipment when you stopped this operation. The person in charge of the equipment signs in this column. This includes accidents, breakdowns, unplanned stops, or changes in location, and so forth.
Any unusual operations and faults on the equipment go on the DA Form d. Completion instructions by block title or column Date. Enter the calendar date the form was started. Fill in as required locally. The dispatcher signs name. Print the name of the person or activity asking for the equipment. For a vehicle, write the place or unit where the operator is to report with the equipment.
For other than vehicles, write the location or place where the equipment is to be operated. The telephone number of the person asking for the equipment. The time the operator is to report to the location in Column b. For extended dispatches, enter the date and time if known that the user expects to return the equipment. For vehicles, put the place, farthest away, that the vehicle is expected to travel. For other equipment, put the location where the equipment will be operating that is farthest from its normal site.
If column f is the same as column b, leave this column blank. The equipment bumper or admin number. Enter the equipment s model identification number for example, enter M35A2. Enter the equipment serial number. For equipment you manage by registration number, put the registration number in this column. Log in the time the equipment was dispatched.
Log in the time the equipment returned. For equipment coming off an extended dispatch, put the day, month, and time of return in this column. When a change of dispatcher takes place during the day, the new dispatcher signs in column m for that item dispatched. When a change of dispatcher takes place at the beginning of the day, the new dispatcher signs in column m on the date line.
Note any towed equipment, that will come back with the prime mover, in this column. Write the noun for the towed equipment here. Make separate entries for towed equipment that will not come back with the prime mover. Treat towed equipment that will not come back with the prime mover as if it were not towed. Complete all columns except the expected time of return.
Identify equipment involved in accidents or unusual circumstances. When more room is needed, use NEXT open line. Line out all unneeded columns, a 1. Chapter 3 Maintenance Forms 3 1. The forms in this chapter help in scheduling, doing, recording, and managing maintenance on equipment.
The forms show the results of inspections, tests, and maintenance performed. They also show the results in diagnostic checks and form the bond between maintenance and supply actions. This chapter provides procedures and examples of maintenance forms used by manual units as well as those units supported by the S t a n d a r d A r m y M a i n t e n a n c e S y s t e m s S A M S. U n i q u e S A M S forms are addressed in chapter In addition to the forms within this chapter, maintenance forms for non standard air traffic control ATC and navigational aid NAVAID equipment, when specified in the equipment s technical publications, will also be maintained.
Examples of non standard equipment are, but not limited to 1 Instrument Landing System ILS and all associated marker beacons. DA Form serves as an identification tag. See fig 3 1. After repair is done, the tag identifies the item as fixed. The DD Form is a record of scheduled and performed unit maintenance including lubrication services. See figures 3 2 through 3 6. DD Form is used to 1 Schedule periodic services on equipment, to include components in a system or subsystem, when the technical manual requires a PMCS service to be performed by unit maintenance personnel.
This form is also used to schedule the following services performed under the supervision of unit maintenance personnel: When these are marked out, schedule services on the next working day. M monthly 1 month service. Q quarterly 3 months service.
S semiannual 6 months service. A annual 1 year 12 months service. E 18 months service. B biennial 2 years service. F quadrennial 4 years service. The interval block on an LO only tells when to schedule the lubes. It does not tell what services to schedule or symbol to use. You may also use subsymbols to explain a service and lube pulled at the same time. To schedule a service, put its symbol in pencil in the date due block with its miles, kilometers, or hours beside it as shown below. Not all services will have miles or hour intervals.
You may not always be able to pull a service when it is scheduled. So you are given a 10 percent variance before or after the schedule of days, miles, or hours. Some services may be too critical to have a variance. When you do the service within the variance, ink in the symbol with the equipment s miles, kilometers, or hours on the date it was scheduled. When a service outside the variance is completed, erase the scheduled symbol and data, and ink in the symbol with data on the actual day the service was completed.
Schedule the next service from the new date. By hours, miles, or kilometers only. Put the miles, kilometers, or hours when the next lube is due in the Remarks block. On a date interval. Put the symbol L on the date block the lube is due. Enter the miles, kilometers, or hours when they apply next to the symbol. When the lube is done, ink in the L and the miles or hours. DD Forms are tied to unit level services and their intervals. The number of DD Forms you need varies, based on the equipment and how and where your maintenance is pulled. Normally, one DD Form covers one piece of equipment.
Several like items may be covered by one DD Form if the services are scheduled and pulled on the same date.
Functional Users Manual for The Army Maintenance Management System (TAMMS) - PDF
Examples of like items are small arms and M11 decons. When scheduling services on more than one item, put each item s serial number in the Remarks block. NMC time is kept only when the equipment has a deficiency defined as not mission capable in the PMCS not mission capable if column. Use the front side of the DD Form to schedule services.
Post this time to the DD Form NMC time on equipment still in support maintenance at the end of a report period will be provided to the owning unit by telephone or other local means. A day is the normal work day for your command. See AR , chapter 4, for missiles. This information will be given to the owning unit at the end of the reporting period and when the equipment is returned. You will keep another separate DD Form on the overall system, which is the system card. Scheduling oil samples on the DD Form is optional when the lab gives you a printout that lists when the next sample is due.
Schedule oil samples in pencil on the DD Form When the sample is taken, erase the symbol and hours from the DD Form and schedule the next sample in pencil. This can include services performed by other echelons or units when the commander so directs. If a commander wants operator or crew services scheduled, put them in the Remarks block. Within remarks section, exact PMCS technical reference will be shown, down to specific paragraph. Within remarks section, normal time required for each PMCS interval will be shown.
Within remarks section, show date of last flight check of navigational aid. Use a signal system to show when a service is scheduled in the current month. A month can be from the first day to the last day of the month e. At the start of each month, put your signals on the date blocks for the service. When the service is pulled, take the signal off the card or move it from the date block to one corner.
Use the following signals: A green signal indicates a lube L is needed. Put a red signal over the right corner of the card when equipment is NMC. For equipment reported as a system in AR , table B 2, use the red signal only on the system card. Take the signal off the card when the equipment is fixed. Low usage is as follows: A f t e r e q u i p m e n t i s placed in the program, all services and lubrications will be combined with the annual service.
Disposition of the DD Form is as follows: Transfer the information from these blocks: The gaining unit reports the equipment s NMC time after the item is added to their property book. DA Form has three major purposes. See figs 3 7 through 3 Operators and crews, first line leaders, mainten a n c e s u p e r v i s o r s, a n d c o m m a n d e r s a r e e q u a l l y r e s p o n s i b l e f o r keeping information current and correct on the DA Form This form is the central record for managing and controlling maintenance as follows: These faults include PMCS, maintenance activityl inspections, diagnostic checks, and spot checks, except as noted in paragraph b 10 below: The DA Form will be used by personnel performing inspections, maintenance services, diagnostic checks, technical evaluations, marine condition surveys on watercraft, and PMCSs, except as noted in 10 below: You may use one DA Form or separate forms for each subsystem.
When used to inspect several like items, the DA Form will list all deficiencies, shortcomings, and corrective action taken. Attach the initial inspection to the DA Form that will be given to the person making the repairs. The DA Form will be used as the worksheet for correcting faults found and reporting any uncorrected unit level faults. Results of the maintenance action will be entered on the DA Form 7 On final inspection by support maintenance to list faults found. Attach the final inspection to DA Form that will be given to the person that performed the repairs.
The repairer will correct all faults found during the final inspection. AR and the individual equipment battle damage technical manuals govern when and how battlefield damage repairs should be accomplished. Make sure you read the instructions that apply to your use of the form. Put 1 of 2 on the first page and 2 of 2 on the second, etc. If faults are found during an operator s or crew s PMCS, it will be given to the maintenance supervisor for action. This includes the DA Form on equipment sent to support maintenance.
The form or a locally used signal will be kept in the equipment record folder to keep the equipment from being dispatched. Forms carrying a status symbol X will be kept until the fault is corrected. Destroy the form only when the next periodic service is done. This situation normally applies to the form used for services on more than one item or when an operator level service is required and must be documented.
If the form lists no faults from previous service, use the same form to show the results of the current service. One copy will be returned with the DA Form that requests repair of the damage. See fig 3 T h e a u t o m a t e d f o r m, P C N A H N 0 0 7, provides a consolidated list of all open work orders, man hours, and work order status. Then, destroy the form. See figs 3 15 through 3 Repairs beyond the unit s authorized capability or capacity. See para 3 7. Fabrication or assembly of items. AR governs this program. The specific FPG identifies mandatory data elements for the forms.
You may use one form for as many items under an NSN as needed. For example, one DA Form might cover 10 rifles or 5 starters or 30 carburetors, etc. AR and the individual equipment battlefield damage repair technical manuals govern how such repairs should be done. Also assign an ORGWON when a nonreportable subsystem of a reportable weapon system causes the weapon system to become inoperative.
Numeric 0 zero is authorized to be used in a UIC. If the sixth position of the ORGWON has a zero 0 or one 1 , it identifies ground or missile maintenance equipment, and whether it is reportable or not. A zero 0 identifies an end item as reportable under AR , or when a command maintenance significant item, selected by a local commander, becomes inoperative. Also assign a zero 0 when a nonreportable subsystem of a reportable weapon system causes the weapon system to be inoperative. A one 1 is used if the item of equipment is not reportable. Also, a one 1 is used if a reportable item needs repair but is not inoperative INOP ; e.
If the sixth position of the ORGWON has a two 2 or a three 3 , it identifies aircraft maintenance equipment, and whether it is reportable or not. Also assign a two 2 when a nonreportable subsystem of a reportable weapon system causes the weapon system to be inoperative. A three 3 is used if the item of equipment is not reportable.
Also, a three 3 is used if a reportable item needs repair but is not inoperative INOP ;e. Copy one then goes back to the organization as a receipt for the equipment. The unit returns copy one when the equipment is fixed and ready for pickup. Equipment owner will be notified when parts are available. Support maintenance will retain copy number 1 and the equipment owner will retain all other copies. The unit will return the equipment and maintenance work request no later than the end of the following work day of being notified by support maintenance.
Destroy when the equipment is returned to the unit. Handle as directed by the local command. For items under a DA approved sampling plan, hold this copy as directed by the plan. See figs 3 17 and 3 MWOs are normally applied by support, depot maintenance, or commercial contractors. The responsible sponsoring agency will ensure that equipment owners know when MWOs apply to their equipment.
The equipment normally does not go to that activity until MWO kits are on hand. If MWO kits are already on hand, the equipment will go with the form. The receipt copy one will be returned to the unit. All other copies of the form stay with the support maintenance activity. When the MWO has been applied. The MWO publication will tell you who the agency is and what address to use. Otherwise, handle as directed locally. Do not use SF Form to report warranty claims. The contractor or dealer will expect to be paid for that work. The WARCO must stipulate, at the time of delivery, that either no non warranty work be done or be prepared to pay for the work.
No other forms are authorized as substitutes or replacements. Performance, part failure, and warranty cost effectiveness can be determined, just to list a few. The DA Form should list the end item in the header blocks blocks 1 Exhibits will be retained until disposition instructions are obtained. Normally, disposition instructions will be in the supporting WTB. When the supporting WTB does not provide disposition instructions, the materiel manager provides disposition instructions to you within 30 calendar days after receiving your WCA. The WCA will be completed at the normal level of repair.
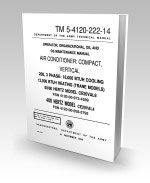
A few WTBs, however, may require that copy three be sent to a separate location or at a different time when special or expedited parts support is needed. Then, dispose of the form. The DA Form is a record of uncorrected faults and deferred maintenance actions on equipment. Deferred maintenance actions are authorized delays for repair or maintenance. Equipment with deferred maintenance does not meet the Army maintenance standard as addressed in AR 1, paragraph 3 1a. That is, an authorized delay for maintenance actions.
This form is not required when an automated system provides you with a list or printout of deferred maintenance and uncorrected faults that includes all elements on the DA Form c. A single form may be used to show deferred faults on such items as long as each fault entry is preceded in column b by the item s administration or serial number. Look for faults that may affect the mission and faults that are overdue to be fixed. For example, look at any dates in column c that have passed or actions that have already been taken. Check on the status of parts on order.
Look for any faults that have been fixed, but not closed out. Check for any faults overdue to be fixed. The status symbol for the NMC condition then changes to an X and the entry can no longer stay on the form. It logs document equipment performance and maintenance activities, as well as provides a historical record of site events. General Instructions 1 Basic log format. Log entries will be clear, complete, and concise. The log documents fact, as perceived by the person making the entry. The use of standard abbreviations and references to substantive records is encouraged in expressing activities in the clearest manner.
Legible entries will be made in ink. All information noted will correlate with related data on other forms, records, and reports. Maintenance activities logged will cite the appropriate technical reference needed to support the entry as a complete, understandable statement. Logs will be kept in the immediate vicinity of the log subject. Exceptions are allowed where this is impractical, but the location will be designated within the maintenance standard operating procedures.
There will be no erasures or deletions of any entered data. Errors will be corrected by one of the following two methods: This method will only be used when the correction can be entered adjacent to or immediately below the erroneous entry. The person making the correction will then note the date and time of the corrected entry and their initials in the margin adjacent to the erroneous entry. Entries in the logs will provide a complete accounting of activities related to facility status, certification, operation, or performance. Entries will include but are not limited to a Arrivals and departures at facilities not manned.
At least one entry will include the purpose of the visit, if not apparent from other entries. The originator will initial the entry in the area provided on the last line of the entry. All serialized log pages will remain in numerical order with any exceptions noted. When starting a new log, the serial number of the last page of the old log will be referenced in the first entry of the new log. The serial number of the first page in the new log will be referenced in the last entry of the old log or in the lower right margin of the last page. The month and year corresponding to the beginning entry on each page of the log will be entered in the month and year block at the top of each page of the log.
All entries will be referenced to date and local time. Entries continued from the previous page need not have a date and time on the continued portion. After last entry of each month, state Last Entry Month of month. At the end of each month, the technician having the primary responsibility for the maintenance of the facility or navigational aid covered by the log, is responsible for DA PAM August. Review will address log procedural or policy discrepancies, technical completeness, detection of facility performance trends, and recurring malfunctions.
Mistakes or unclear entries will be corrected by an additional entry referenced to the erroneous entry by date and time. The white page s will be removed for filing at the maintenance office. Retain facility maintenance logs on file a minimum of 5 years from date of last monthly entry, or until no longer needed. Enter the UIC of the support activity that will receive, hold, or Work on the item for you. Enter the Julian date the form was initiated. Enter the UIC of the owning unit or organization. Mark the block to show the use of the form. If form is being used for other than the options indicated in Block 4 e.
Enter the NSN of the item. Print the noun abbreviation of the item to be exchanged. Enter the priority designator PD that applies to the action. The unit or organization listed in Block 3 normally assigns the PD. When the form supports a customer maintenance request, use the PD of the maintenance request. The commander or the commander s designated representative signs when a PD of 01 through 10 is in Block 7.
Enter the maintenance work order number when a PD of 01 through 10 is taken from a maintenance request. Enter the noun abbreviation of the end item for the part or component in Block 6. Enter the model number of the end item.
- Video Rose and Mark Spark.
- Coalescence (I Found My Heart in San Francisco Book 3)!
- Blog Archive;
- Invitation To A Dance Hall.
- Carmella Jackson: Manifest Vampire, Kindle Edition;
- Air conditioning, refrigeration, and air filtration systems training manuals.
- Functional Users Manual for The Army Maintenance Management System (TAMMS).
Enter the serial number of the end item. Briefly describe the problem. When the form is used as a receipt, the support unit will enter the Julian date. The person who receives the item signs. Print the word Yes for NMC condition. The facility that will repair the item enters the maintenance work order number. The person receiving the item for repair initials in this block. The person doing the work enters the Julian date that the work was finished. The person doing the work initials in this block. Completion instructions by block title Use either the blocks at the top or the bottom of the card.
Put the last two digits of the calendar year in the shaded box at the upper left or lower left of the card. Enter the registration number, if the equipment has one assigned, or the serial number. Enter the equipment s administration number bumper or locally assigned number. If the equipment does not have an assigned administration number bumper or locally assigned number , pencil none assigned in this block. Put the noun abbreviation in this block.
If the item is a system or part of a subsystem, enter either system or subsystem as applicable. Enter the model number;for example, M Use the exact model format listed in AR Assigned To. Enter the name of the unit or organization owning the equipment. In pencil, annotate any maintenance information that will be needed in the future or on the replacement form for the next year.
This information may include service symbols, dates for current and next year, and warranty information. Your Warranty Control Office or Logistics Assistance Office can assist you with warranty data for specific pieces of equipment. Use it when filling out the DA Form b. Antifreeze entries will be made in the Remarks Block for equipment under warranty or using commercial or arctic antifreeze. For additional information, see TB c. Cooling systems serviced with antifreeze, Mil A , require the degree of protection, the condition of the cooling system, and the use of antifreeze extender, Mil A , recorded in this block.
Leave blank or use as needed locally. Indicate services scheduled with pencil entries and services completed with ink pen entries. When support gives you a day by day breakout of NMC time, mark the days in the date block. For equipment with hourmeters or odometers, show the total time of miles on the equipment at the last meter change. For example, Odometer replaced at 23, miles, new reading 0 zero miles or Hourmeter replaced at 1, hours.
- survivalebooksblog: U.S. Army Technical Manuals Series 5 Page 2;
- The Oxford Virus?
- Parties in Congress.
- Blog Archive.
- U.S. Army Technical Manuals TM Series 5.
- 5,000 U.S. Military Technical Manuals?
New reading 5 hours. The - replaced at number is the total cumulative hours or miles on the equipment at the time the meter was replaced. The new reading number is the hours or miles on the new meter when you put it on the equipment. The replaced at and new reading numbers will be in pencil.
This information is needed for the DA Form Usage report and others. Show day by day breakout of NMC time. Mark the days in the date block. Completion instructions by block title Put the last two digits of the calendar year in the shaded box at the upper left or lower left of the card. List each subsystem in the system. AR tells you what the subsystems are. Put the serial number or other identifying number in pencil beside the subsystem.
NMC time for all subsystems will be combined. Show day by day breakout of NMC time for system. Enter the number of items being recorded in the Remarks block. For example, Pistol 1 Enter the noun of the item. When using the form to show services on more than one nonreportable item, serial numbers or administration numbers will be listed in ink in the Remarks block on the front side of the form.
At the end of the year, the back side of the form will be used. The serial or administration numbers do not require recopying on the reverse side of the DD Form Enter the name of the unit to which the equipment belongs. Enter the noun abbreviation and the model of the equipment. For watercraft, use the noun abbreviation and Hull Design Number. Enter the serial or registration number. For watercraft, enter the DA Hull Number. When a deficiency or a shortcoming is found, enter the miles or kilometers on the equipment s odometer at the end of the day s dispatch or operation.
Round to the nearest mile or kilometer. Leave blank if the item does not have an odometer or if no faults are found. When a deficiency or a shortcoming is found, enter the meter reading at the end of the day s dispatch or operation. Leave blank if hours do not apply to the equipment or if no faults are found. Enter the calendar date the deficiency or shortcoming was found.
Use the same DA Form for more than 1 day. When no faults are found, this form can be used for more than 1 day even if form was used for concurrent PMCSs, i. When two TMs cover an item, put the second TM number and date in the second number and date block. Then, put the latest change date in the TM date block. When a deficiency or shortcoming is found, the operator or supervisor signs and enters rank.
A signature in this block keeps the form from being used past current dispatch. Maintenance supervisor or the commander s designated representative will sign when corrective action is taken. For a missile system and missile subsystems reported under AR , chapter 4 , enter the time when item was found to be NMC. Put the PMCS item number that applies to the fault listed in column c. If the PMCS has no item numbers, list the page, paragraph, or sequence number.
But, you will list them if you find a problem with one of them. For those faults not covered by the PMCS, leave this column blank. Enter the status symbol that applies to the fault or deficiency. Briefly describe the fault. Skip one or two lines between faults. This will give maintenance room to note actions they take. When more than one TM covers the equipment, draw a line under the last entry for one TM. Under the line, write the TM number of the manual you will use next. After you finish the PMCS and list all faults you cannot fix, give the form to the maintenance supervisor.
When using one DA Form for more than one item of equipment, enter the serial or administration number for the item with the fault. Write the fault on the line below the serial numbler. Explain corrective actions taken. The mechanic initials any faults that have been fixed. The initials will go on the last line for the entry in column d. The maintenance supervisor will review the faults corrected and those still not fixed to decide what other action is needed.
For quality control, the inspector or a designated representative will check all corrected status symbol X faults. The inspector will then initial the status symbol. When no faults are found, this form can be used for more than 1 day even if the form was used for concurrent PMCSs, i. A signature in this block keeps the form from being used past the current dispatch. The commander or the commander s designated representative will sign name and rank when making a status symbol change or changing from an X to a CIRCLED X status symbol for one time operation.
For missile system and missile subsystems reported under AR , chapter 4 , enter the time when item was found to be NMC. Put the TM item number that applies to the fault listed in column c. Changing of status symbols should only be done when the equipment is crucial to the mission.
Common sense must be used. If you find a fault that can be repaired, stop the PMCS and correct the fault. This will give maintenance room to note actions taken. Print Cleared for limited operations, and the specific limits under which the equipment can be operated. For example, limits may involve speed, type of mission, distance, weather, or time. The change may affect a subsystem of a system listed in AR If so, make sure the limits include the part of the mission the system can no longer do.
When a deficiency is corrected immediately or changed to a CIR- CLED X, entries in blocks 4 and 5 will be made at the end of the dispatch or operation. The commander or the commander s designated representative initials for limited operation entries. The initials will go on the last line of the entry. For watercraft, enter the DA hull number. For more than one item, leave blank. Enter the calendar date the service is performed. Enter the type of inspection or service to be done lubrication, monthly, quarterly, semiannual, etc. For missile systems and missile subsystems items reported under AR , Chapter 4 , enter the time when item was found to be NMC.
But you will list them if you find a problem with one of them. Do not enter faults on the DA Form that you have repaired. Continue the PMCS to ensure no other faults exist. Briefly describe uncorrected faults. Explain corrective action taken. For equipment needing a DA Form , note repair work done and parts replaced. If parts are needed, the PLL clerk will order them and enter the document numbers. The commander s designated representative will decide what maintenance can be delayed.
Faults that do not affect the operation of the equipment and the operator s safety can be deferred because: The person taking the action or transferring the information initials other entries. For quality control, the inspector or commander s designated representative will check all corrected status symbol X faults to ensure proper repairs have been completed.
Completion instructions for DA Form used for services on more than one like item 1 Organization. Enter the calendar date the service is performed or the shortcoming was found. Then, put the latest change date in TM date block. For missile systems or missile subsystem items reported under AR , Chapter 4 , enter the time when item was found to be NMC. Write the fault on the line below the serial or administration number. Continue the PMCS to ensure that no other faults exist.
If properly repaired, the inspector or the commander s designated representative will initial the status symbol. Completion instructions for DA Form used for battlefield damage assessment and repair Note: Enter the miles or kilometers on the equipment s odometer as of the date in block 5. Leave blank if the item does not have an odometer. Enter the meter reading in hours as of the date in block 5. Leave blank if hours do not apply to the equipment. Enter the calendar date.
Enter the letters BDAR. When the repair or replacement has been accomplished, the person doing the job will sign name and enter rank. The maintenance supervisor or the commander s designated representative will sign name and rank. This is to ensure that when corrective actions are taken, no safety faults still exist that would endanger the operator or cause further damage to the equipment. If more than one deficiency or shortcoming is noted, leave enough room between entries to allow for corrective action taken to be annotated.
We are offering our package for only $45 which includes free shipping also.
Explain actions taken to correct or repair the fault. Note any parts replaced, parts ordered, and work done. The person taking the action initials here. Prepare the DA Form in triplicate. Enter the rounds fired as of the date in block 5. Leave blank if rounds fired does not apply to the equipment. Enter the letters ECOD. Enter name, rank, duty phone number, signature, and organization of the inspector preparing the DA Form 8b Time.
In columns a, b, c, d, and e, enter required information as instructed in the following steps. Enter the fault number. Enter the status symbol that applies to the fault. Enter each fault detected during the technical inspection that requires repair or replacement to restore equipment serviceability. Enter the maintenance action repair or replace required to correct the fault entered in column c. Enter the man hours required to correct the fault identified in column c. Print Date of Manufacture: Print Time Since New: If an outstanding modification work order has not been applied to the equipment, print Outstanding Modification Work Orders.
List all applicable modifications that have not been accomplished. Next to each modification, enter the man hours required to apply the MWO. Print Total Man hours to Repair followed by the total estimated man hours required to restore the equipment serviceability. Print Total Man hour Cost. In column d, enter total hours required to do the repair multiplied by the current local labor rate. In column e, enter total dollar cost. Print Repair Cost Factor followed by the repair cost factor percentage and dollar factor, if applicable cited in the TB listed in step 7.
Print Total Cost of Replacement Parts followed in column e by the total cost of required replacement parts Total of Step 9. Enter total in column e. Print the name of the unit or activity asking for the work. Briefly describe the equipment fault or the action taken. Action includes MWO to be applied, one time inspection, etc.
Enter the Julian date the request for maintenance came in. Enter the Julian date the repair action started. Enter the Julian date when the item was fixed. Block 28M of the DA Form gives you that information. Blocks BLK 1, 5, 6, 7, 10a, 10b, 11,12, 13, 15, 16, 20, and 24 are mandatory if equipment is inoperable. Enter the UIC of the customer that owns the equipment.
Enter the name of the unit identified by the UIC in block 1a. Enter the phone number of the unit identified by the UIC in block 1a. If not, leave this block blank. Enter the Type Maintenance Request Code. Appendix B, Table B 20, lists the codes. Enter the Identification ID Code as shown below that identifies the type of number you will enter in Block 7. Enter the National Stock Number or appropriate number identified in block 6.
Enter noun nomenclature of item. Enter organization work order number or organization document number. Enter the end item code EIC. Enter the serial number of the item in Block 9. For nontactical wheeled vehicles, use the registration number. For ammunition, use the lot number. Leave blank if the form is used for more than one item. Leave blank if the equipment has more than one serial number. Mandatory entry if equipment is INOP. Enter the number of items. Enter the Priority Designator.
about of parts
Leave blank if no failure occurred. Enter the miles or kilometers from the odometer on the equipment beside the M or K. If the equipment has no odometer, leave blank. Enter the hour reading to the nearest hour beside the H from the hour meter mounted on the equipment. If the equipment has no meter, leave blank.
Enter the total equivalent full charge EFC rounds fired beside the R. See the item s DA Form If rounds do not apply to the equipment, leave blank. Enter the project code if one has been assigned. If not, leave blank. If not required, leave blank. Enter Y or N to indicate whether equipment is still under manufacturer s warranty. If Y, submit one work request for each serial numbered item.
Enter code for level of work from Table B The commander or the commander s designated representative will sign for all priority 01 through 10 requests. This signature approves the use of the PD. Using the information in column c of DA Form , briefly describe the fault or symptoms.
Do not ask for general or specific repair of parts to be replaced; for example, do not tell support to replace the hydraulic system or repair as needed. When the form is asking for work on more than one item with the same NSN, list the number of items, their serial numbers if they have serial numbers , and anything else support will need. Put the NSN on the last line of block You will also find the codes listed as part of the item s Source, Maintenance, and Recoverability SMR code in the parts manual.
If you need more room, use a DA Form e. When the form is requesting standard repair after a battle damage expedient has been applied, print BDAR in bold letters before describing the fault or symptoms. When the item in block 7 needs onsite or deferred maintenance, support wil note that action here. Shop office NCO will make one of these entries for onsite or deferred work: Block 35a will be filled in by support only when the onsite repair is started or the deferred item is brought back to support. The receipt copy will be sent to the support unit.
The owning unit keeps all other copies until the onsite repair is started or deferred item is taken back to support. The person sending in the DA Form enters first initial and last name in this block. Enter page numbers as required.